Die cut is a process used in printing and packaging to cut out different shapes using machines. Die-cut printing allows for precise measurements to be specified, and the machine will cut them to the exact dimensions.
This level of precision is fundamental in product packaging design, where a consistent, professional look needs to be achieved every time.
What is a Die Cut Mean?
Die cuts begin with a die. A die is a piece of metal that has sharp edges. Die cuts are similar to cookie cutters because the shape of the metal object that is cut into a die is the same as the shape of the material that is cut into the die. There are a few different types of dies. Steel-rule dies, for example, are very sharp but are protected by plastic or foam to keep them safe.
Steel-rule can be used to cut thicker packaging material or to cut a pile of thinner packaging material at once. Thicker metal dies are not as sharp as steel-rule dies and are not suitable for cutting very dense material. Thicker dies are lighter, easier to store and have no foam or plastic around the dies for safety.
Die Cut History: Why is it Called Die Cutting?
The word ‘die’ is derived from the Middle English word, ‘de,‘ meaning “to place or place,” which is believed to be derived from the Latin word “datum,” which means “to give,” and “to put,” meaning “to put or place.”
In the 1300s, die cutting was mainly used for casting or stamping metal coins. In the 1800s, the mass production of items of similar size and shape began to take over, and the old term’ die’ was used to indicate that it was ‘created by machines.’
The term ‘die cutting’ was first used in the 1800s as a way to create more accurate and precise shoe sizes. Shoes were initially made of leather, and the soles were cut by hand. This was a labor-intensive process that often resulted in errors and poor fit. With the invention of the die-cutting machine, shoes could now come in standard sizes, which we now take for granted.
The Role of a Dieline In The Custom Die-Cut Process.
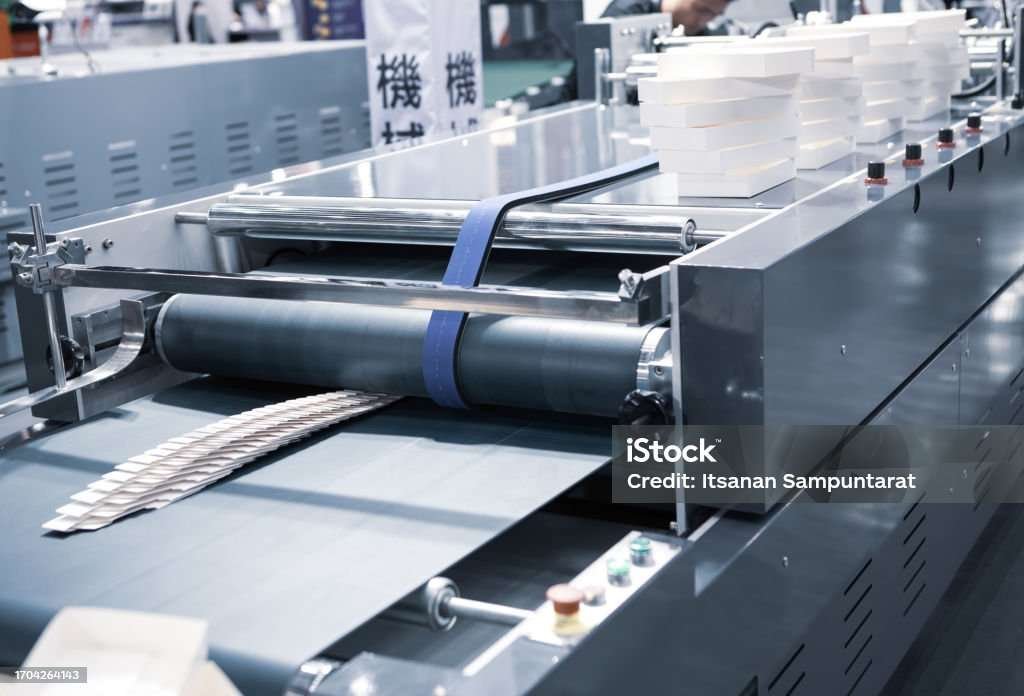
Before any printed material can be cut, a die cut mean is necessary. This is where the decline comes into play. A dieline is an essential part of the custom die-cut printing process. It outlines the shape and size of the packaging box before any cutting can occur.
With so many shapes available in the packaging industry, if you dream of it, you can be sure that a custom packaging manufacturer will be able to cut your material into any suitable shape.
What is Traditional Die Cutting?
Traditional die cutting uses a thin, sharp steel blade in a particular pattern or shape, depending on the product being cut (think cookie cutters). Die-cut printing, is the process of cutting through materials (e.g., paper or label stock) on a die printing press to create unique shapes and designs.
What Is Digital Die Cutting?
Digital Die Cutting requires a computer-controlled knife that cuts the shape. The knife is controlled by a cut file, which the computer & cutter when cutting. Digital die cutting allows you to have any shape you need on the fly. This eliminates the need for a traditional ‘cookie cutter’ die. This means a meagre setup cost to the customer and an immediate turnaround time. Our cutter includes an integrated camera that corrects the shape to cut according to the print. Real-time print error correction is possible. The downside of this process is that it is slower and more expensive for high-volume items but is suitable for low to medium-run.
What Materials Can Be Die Cut?
While die-cutting can be applied to a broad range of materials, it is most effective on materials with low dimensional stability. In our experience, paper is the most common material to be die-cut for applications such as cards, vinyls and stickers. Films, fine plastics and magnets can be die-cut, but testing is required.
What Are Die-Cut Printing’s Design Elements?
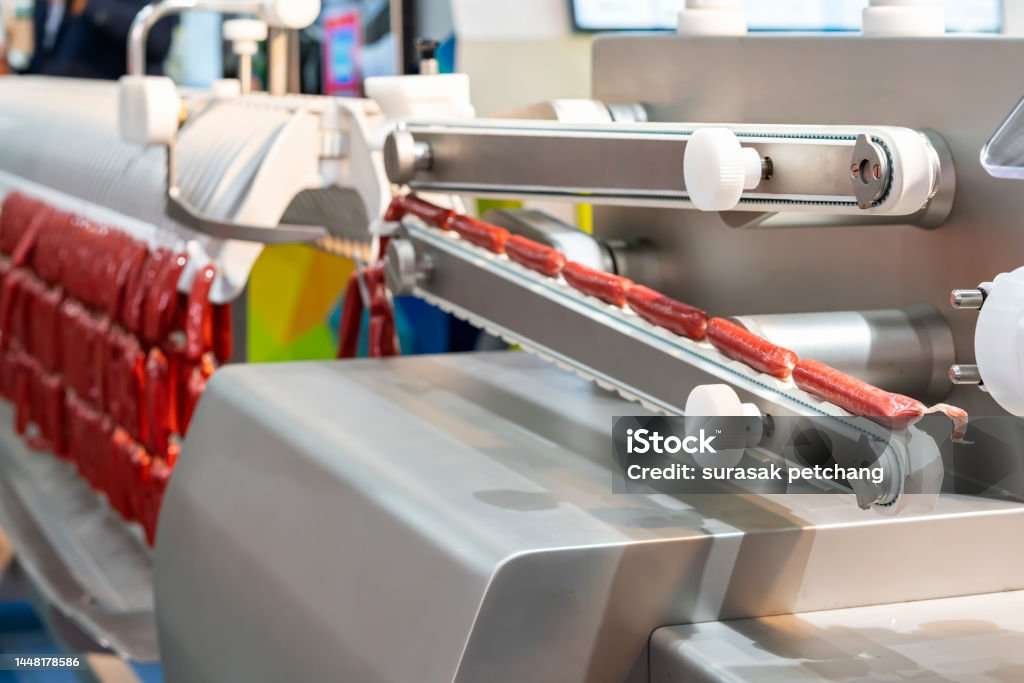
Dies come in a wide variety of sizes and styles so that you can find the perfect die cut for your project or event. Die cutting can add a 3D element to your paper project, depending on the design and shape you choose. You can go for basic shapes, flowers and animals, or almost anything you can imagine. A die-cut design can add either a decorative element or a functional one to your design. For example, a die-cut silhouette can be used to draw attention to your design, or you can use a semi-moon thumb hole for an open-ended envelope.
Die cutting can be divided into three main types: blanking, drawing, and broaching. The kind of die-cutting you use depends on your project and your product vision. The most common die-cutting methods are blanking and drawing.
1. Blanking is the process of cutting flat material by clipping the outside edge of the material to make it look more flat.
2. Drawing is the process of pulling material through the die-cutting machine to a specified length. This method is usually used for thin,/or long products.
3. Forming is the process of shaping the raw material into a cylindrical shape. This method is often used in conjunction with drawing to create the cylindrical part of custom packaging.
4. Coining is the process of making circular holes in the raw material by applying pressurized force. Broaching is the process of using multiple rows of “teeth” to cut material the steel die would not be able to cut.
There are many different types of die cutting in digital and offset printing, but this will provide an overview of the most common types used in packaging. Die-cutting services are also available depending on your requirements.
What To Consider for Die Cut Labels Types Of Die Cutting?
Flatbed Die Cutting
Flatbed die cutting (also called steel rule die cutting) is the most common type of die cutting in packaging. It uses flatbed die-cutting presses and custom dies to produce its customized shapes (dies). This type of die-cutting is suitable for thicker materials, larger parts of packaging or even short production runs.
Rotary Die Cutting
Rotary die cutting is a die cutting used for higher volume production runs. It uses cylinder-shaped dies to transform flexible material into customized boxes or packaging. Rotary die cutting is ideal for high-volume runs and designs that require exact accuracy.
What is Die Cutting in Printing?
Die cutting is heavily dependent on steel rule dies, which have been used for over 150 years to carve and set dies into wooden blocks. The modern die production process is based on computer-aided design software that creates the die’s layout.
Precision measurements
These are obtained by carefully examining the dimensions and parameters of the die. The base of a steel rule die is a flat sheet of wood or metal, while the base of a rotary die is a curved sheet of metal or wood that sits on top of a metal cylinder.
Plasma cutting
It is the process of laser cutting into the base material to create the pattern for placing steel blades in the flatbed die cutter. Kerf cuts (also known as precision cuts) are required before blades can be installed on the flatbed die.
Blade forming
It is the process of programming CNC machines to create the exact kerf shapes needed for the final shaping of the blades. Finally, slotting is the process of fastening the steel rule to the base of the flatbed die to make the cutting tools for the die.
Ejection rubber
The die has a rubber ejection strip that allows the cut piece to be removed without damaging the material or tearing, fraying, or holding the steel rule in place during the cut.

Tips for Die Cutting
- Avoid sharp edges and angles to avoid tearing the matrix when you remove it after die cutting
- Make sure there’s enough space between your home and your label’s edge to prevent tearing
- Make sure the artwork you’re using in your label design bleeds past the label’s edges by a minimum of 1/16″
- Ensure you don’t accidentally include blank spaces in your design
- Add your shape’s die line correctly to your Adobe Illustrator document
- Please create a new die line layer and color it differently from the rest of your background